Benefits of Regular Warehouse Cleaning
Regular warehouse cleaning provides numerous advantages beyond just a tidy workspace. Cleanliness is essential for maintaining a safe and efficient environment for both employees and equipment. Dust and debris can accumulate quickly in a warehouse setting, leading to potential hazards and reduced productivity. By implementing a consistent cleaning schedule, you can ensure that your warehouse remains organized and free of clutter, promoting a more streamlined workflow.
In addition to safety concerns, regular cleaning also plays a crucial role in prolonging the lifespan of your equipment and machinery. Dust build-up can cause wear and tear on vital components, leading to increased maintenance costs and downtime. By keeping your warehouse clean and dust-free, you can minimize the risk of breakdowns and malfunctions, ultimately extending the longevity of your equipment and maximizing operational efficiency.
Importance of Maintaining Clean Equipment
Regularly cleaning equipment in a warehouse setting is an essential task that often gets overlooked but plays a crucial role in maintaining the overall efficiency and longevity of machinery. During my years of working in warehouse management, I have witnessed firsthand the positive impact that a clean equipment maintenance routine can have on operations.
Clean equipment not only operates more smoothly but also helps to prevent breakdowns and costly repairs. When equipment is kept free of dust, dirt, and debris, it functions optimally, reducing the risk of malfunctions and ensuring that operations can continue running smoothly without unexpected downtime.
Prevention of Dust Build-Up
During my years working in various warehouses, one aspect that consistently proved crucial for the smooth operation of equipment was the prevention of dust build-up. Dust accumulation may seem harmless at first glance, but its effects can be far-reaching and detrimental. The presence of dust particles can infiltrate machinery components, causing friction and hindering performance. Additionally, dust can clog filters and ventilation systems, leading to overheating and potential breakdowns, all of which can disrupt workflow and result in costly repairs.
By implementing a regular cleaning schedule and incorporating dust control measures, such as proper ventilation and air filtration systems, warehouses can significantly reduce the risk of dust build-up. Not only does this ensure the longevity and efficiency of equipment, but it also promotes a healthier work environment for employees. Prevention of dust build-up is not just a matter of cleanliness; it is a proactive approach to safeguarding the functionality and longevity of machinery, ultimately contributing to the overall productivity and success of the warehouse operations.
Reduction of Wear and Tear on Machinery
Regular maintenance and cleaning of machinery is crucial for reducing wear and tear. When equipment is not properly cleaned, dirt, dust, and debris can accumulate, leading to increased friction and strain on moving parts. This can result in premature wear on components, causing them to break down sooner than expected. Additionally, neglecting to clean machinery can also lead to the build-up of contaminants, which can further accelerate the deterioration of equipment.
From my years of experience working in warehouse operations, I have seen firsthand the impact that regular cleaning can have on reducing wear and tear on machinery. By implementing a consistent cleaning schedule and proper maintenance routines, we were able to prolong the lifespan of our equipment and minimize the need for costly repairs or replacements. This proactive approach not only saved us time and money but also ensured that our operations ran smoothly without unexpected breakdowns or disruptions.
Minimization of Rust and Corrosion
One key benefit of regular warehouse cleaning that is often overlooked is the minimization of rust and corrosion on machinery and equipment. Over time, dust and debris can accumulate on surfaces, creating the perfect breeding ground for rust to develop. This not only affects the appearance of the equipment but can also lead to operational issues and potentially costly repairs. By staying proactive with cleaning schedules and ensuring that surfaces are kept free of buildup, the risk of rust and corrosion can be significantly reduced.
I have seen firsthand the impact that rust and corrosion can have on machinery within a warehouse setting. Neglecting to keep equipment clean and free of contaminants can result in not only aesthetic issues but also functional problems that can disrupt operations. By prioritizing regular cleaning and maintenance routines, warehouses can protect their investments in equipment, prolonging their lifespan and avoiding unnecessary downtime due to rust-related issues.
Improvement of Air Quality
Ensuring optimal air quality within warehouse facilities is a critical aspect of overall operational maintenance. Regular cleaning and maintenance of ventilation systems, air filters, and dust collection systems are essential in mitigating airborne contaminants such as dust, mold, and pollutants. By maintaining a high standard of air quality, potential health risks to employees can be significantly reduced, fostering a healthier and more productive work environment.
Furthermore, improved air quality can also lead to a decrease in equipment downtime and a longer lifespan for machinery. Dust and debris in the air can settle on equipment, causing malfunctions and reducing efficiency. By proactively managing air quality through regular cleaning practices, the risk of equipment damage and operational disruptions can be minimized, ultimately contributing to a more sustainable and cost-effective warehouse operation.
Prevention of Fire Hazards
I once witnessed a warehouse fire that broke out due to accumulated dust and debris near a machine. The incident left a lasting impact on me as I saw the immense damage it caused to equipment and inventory. This firsthand experience highlighted the critical importance of regularly cleaning warehouses to prevent fire hazards.
Furthermore, neglecting the cleaning of equipment and work areas can lead to flammable materials building up over time, increasing the risk of fires breaking out unexpectedly. It is essential for businesses to prioritize fire safety by implementing regular cleaning routines to remove dust, debris, and other combustible materials that could potentially ignite and cause devastating losses.
Enhancement of Employee Safety
Ensuring employee safety in a warehouse environment is paramount for a smooth and efficient operation. Regular cleaning not only improves the overall cleanliness of the workspace but also significantly reduces the risk of accidents or injuries due to slippery floors or obstructed pathways. By maintaining a clean and organized warehouse, employees can navigate through the space with ease and without the fear of potential hazards.
Furthermore, a well-maintained warehouse also promotes a culture of safety among employees. When the workspace is clean and clutter-free, employees are more likely to adhere to safety protocols and guidelines. This instills a sense of responsibility and mindfulness when it comes to maintaining a safe working environment for themselves and their colleagues. Ultimately, prioritizing employee safety through regular cleaning practices leads to a more productive and harmonious workplace for all.
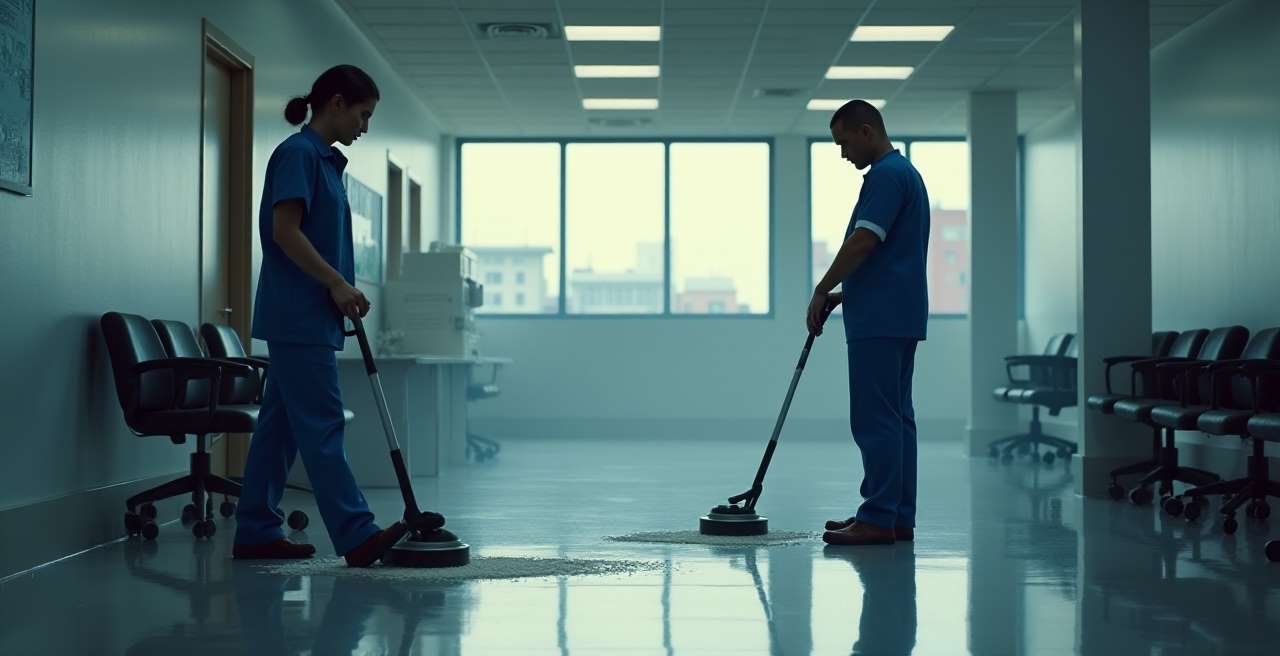
Extension of Equipment Lifespan
Regular cleaning and maintenance of equipment play a crucial role in extending its lifespan. Neglecting this aspect can lead to premature wear and tear, resulting in frequent breakdowns and costly repairs. By implementing a proactive approach to cleaning, such as scheduled maintenance routines and thorough inspections, businesses can significantly increase the longevity of their machinery.
In my years of experience working with various companies, I have witnessed firsthand the impact of neglecting equipment maintenance. Those who prioritize regular cleaning and upkeep not only benefit from prolonged equipment lifespan but also enjoy improved operational efficiency and reduced downtime. It is essential for businesses to recognize the long-term cost savings and operational advantages that stem from investing time and resources into maintaining equipment properly.
Reduction of Maintenance Costs
Regular maintenance costs can quickly add up, especially when dealing with equipment that is not properly cleaned and maintained. Over time, the accumulation of dirt, dust, and debris can lead to premature wear and tear, necessitating frequent repairs and replacements. By implementing a proactive cleaning schedule, businesses can significantly reduce the need for costly maintenance interventions.
A clean working environment not only improves the longevity of equipment but also enhances its efficiency and functionality. When machinery is free from dirt and grime, it operates smoothly and experiences fewer breakdowns, resulting in reduced downtime and maintenance expenditures. Investing time and resources in regular cleaning practices can ultimately lead to substantial savings in maintenance costs in the long run.
Prevention of Contamination
Regular cleaning of warehouses and equipment is crucial in the prevention of contamination. Over time, dirt, dust, and debris can accumulate on surfaces and machinery, providing a breeding ground for bacteria and other harmful contaminants. This can pose a serious risk to the quality and safety of products stored or processed in the warehouse. By maintaining a clean and hygienic environment, companies can significantly reduce the likelihood of contamination occurring and uphold high standards of product integrity.
Contamination can also result from neglected maintenance practices, such as failing to clean equipment regularly or properly. Dust and grime that build up on machinery can mix with products during processing, leading to contaminated batches and potential health risks for consumers. By prioritizing cleanliness and implementing strict maintenance routines, businesses can safeguard against contamination issues and ensure the consistent delivery of safe and high-quality products to customers.
Compliance with Health and Safety Regulations
Ensuring compliance with health and safety regulations is a fundamental aspect of maintaining a warehouse facility. Adhering to these regulations not only protects the well-being of employees but also helps to avoid potential legal consequences. By implementing proper cleaning protocols and safety measures, the risk of accidents and injuries can be significantly reduced within the warehouse environment.
Regular inspections and audits play a crucial role in upholding health and safety standards in the workplace. By conducting thorough checks on equipment, storage areas, and safety procedures, potential hazards can be identified and addressed promptly. In my experience, prioritizing compliance with health and safety regulations has not only fostered a safer work environment but has also increased overall efficiency and productivity in the warehouse setting.
Enhancement of Overall Operational Efficiency
Maintaining a clean and organized warehouse plays a pivotal role in enhancing overall operational efficiency. Cluttered spaces can lead to misplaced inventory, causing delays in order fulfillment and increasing the risk of errors. By regularly cleaning and organizing the warehouse, it becomes easier for employees to locate items quickly, thus streamlining the picking and packing process.
Furthermore, a clean and well-maintained warehouse also promotes a safe working environment, reducing the likelihood of accidents or injuries. When the space is free from clutter and hazards, employees can move around more freely and focus on their tasks without unnecessary distractions. This not only contributes to a smoother workflow but also improves employee morale and productivity.
Positive Impact on Company Image
Maintaining a clean and organized warehouse not only reflects positively on the company’s image but also conveys a sense of professionalism to clients and visitors. When a warehouse is well-maintained and free of clutter, it gives the impression of efficiency and attention to detail, which can instill confidence in customers regarding the company’s quality standards.
Furthermore, a clean and tidy working environment can also boost employee morale and productivity. When employees work in a space that is well-organized and free of debris, it creates a positive atmosphere that can enhance teamwork and overall job satisfaction. This, in turn, can have a ripple effect on the company’s image as satisfied employees are more likely to represent the company in a positive light to customers and partners.